Quality Fences Are Better Than Cheap Fences in the Long Run
When we’re planning to install a new fence, it’s tempting to choose the lowest-priced option to save money upfront. But we’ve learned through years of experience that this approach often leads to substantially higher costs over time. What appears to be a smart financial decision initially can quickly turn into a costly cycle of repairs, replacements, and ongoing maintenance. Let’s explore why investing in quality fences and premium materials makes more economic sense.
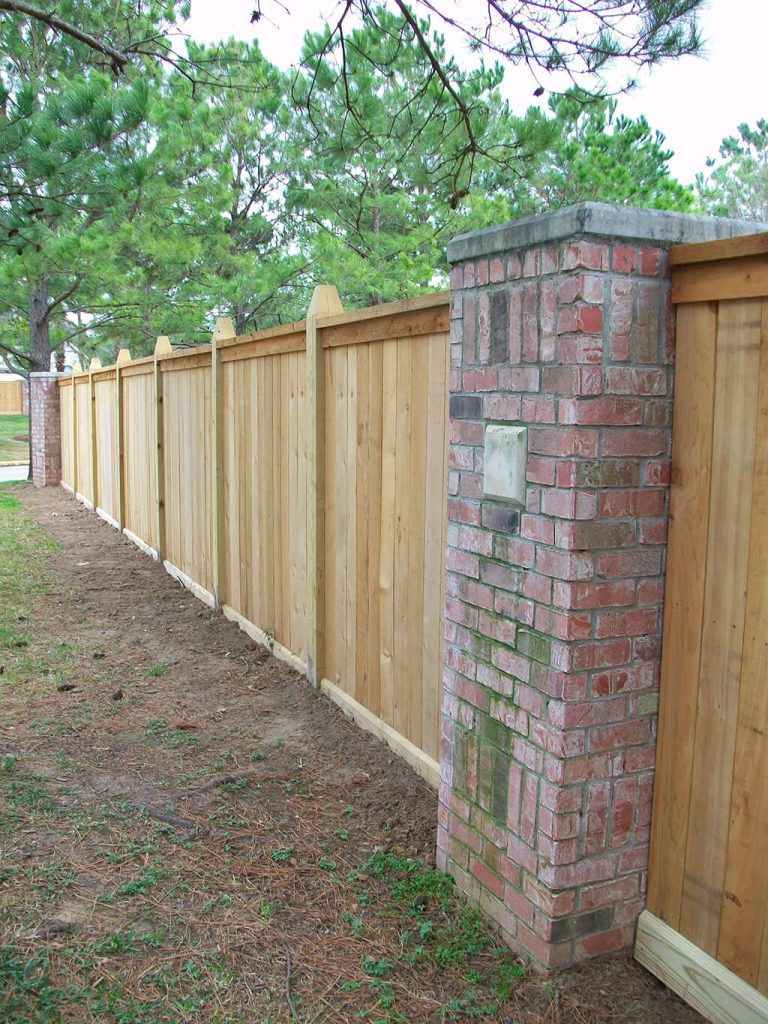
Key Points
- Low-quality fence posts rot within 2-3 years, while premium materials typically last 15-20 years with minimal maintenance.
- Cheap fencing requires frequent maintenance treatments every few months versus annual treatments for quality fences.
- Inferior materials need constant repairs and replacements, leading to maintenance costs that exceed initial purchase savings.
- Quality fences professionally installed can last 20-30 years, making them more cost-effective despite higher upfront costs.
- Budget fencing often requires complete section replacements rather than simple repairs when components fail.
The Hidden Costs of Cheap Fences vs. Quality Fences
While budget fencing materials may seem attractive due to their lower upfront costs, they often lead to significant expenses down the road through premature deterioration, frequent repairs, and early replacement needs.
We’ve seen countless examples of low-quality fence posts rotting within just 2-3 years, cheap metal components rusting through, and inferior-grade lumber warping beyond repair.
These issues typically emerge just as the limited warranty expires, leaving us responsible for costly fixes.
When we factor in the labor costs for repeated repairs and full replacement cycles, we’re looking at 2-3 times the initial investment over a ten-year period.
The true cost of cheap fencing multiplies over time, as repair and replacement expenses can triple your initial spending within a decade.
Quality materials, while more expensive upfront, typically last 15-20 years with minimal maintenance, making them the more cost-effective choice for our long-term property investment.
Vinyl fencing materials offer exceptional durability and resistance to rotting, rusting, and warping, making them an excellent investment for long-term cost savings.
Quality Fences vs. Price: Understanding Fence Material Grades
When we examine fencing materials, we’ll find significant differences between premium and budget options with regard to durability ratings, material thickness, and protective coatings. We need to understand how manufacturers grade their fence materials using industry-standard metrics like gauge measurements for metal and lumber grades for wood. These grading systems help us make informed comparisons between budget-friendly options and higher-quality materials while considering long-term performance and safety requirements. Since 1924, the American Lumber Standard has provided standardized grading rules to help determine the structural integrity and aesthetic quality of wood fencing materials.
Premium vs. Budget Materials
Because material quality directly impacts a fence’s longevity and performance, understanding the differences between premium and budget options is essential for making informed decisions. Premium materials like cedar heartwood, powder-coated aluminum, and marine-grade hardware offer superior resistance to rot, rust, and weathering. These materials maintain their structural integrity and appearance far longer than their budget counterparts.
Budget materials, including pressure-treated pine sapwood, galvanized steel, and standard hardware, can deteriorate more quickly when exposed to environmental stressors. While they’re less expensive initially, we’ve seen these materials require frequent repairs and earlier replacement. When we factor in maintenance costs and replacement frequency, premium materials typically provide better long-term value despite higher upfront costs.
Let’s consider our climate and specific property needs when choosing between premium fences and budget options.
Grading Standards for Fencing
Since fence materials come in distinct quality grades, understanding these standardized classifications helps homeowners make cost-effective choices. We recommend familiarizing yourself with industry grading systems like the American Wood Protection Association’s (AWPA) standards for treated lumber and the American Society for Testing and Materials’ (ASTM) ratings for metal fencing.
Premium-grade materials typically carry Grade 1 or “select” designations, offering superior durability and aesthetics. Mid-grade options, often labeled Grade 2 or “quality,” balance performance with affordability. Economy-grade materials, marked as Grade 3 or “standard,” meet basic requirements but may have visible defects and shorter lifespans.
Let’s always verify that our chosen materials meet local building codes and manufacturer warranties, ensuring we’re investing in fencing that provides reliable, long-term value.
Common Problems With Low-Cost Fencing Options
While low-cost fencing materials may seem attractive for their initial savings, they often lead to numerous problems that can compromise safety, aesthetics, and long-term value. We commonly see thin metal posts that bend under stress, low-grade wood that warps and rots prematurely, and chain link that rusts through within a few seasons. These issues create weak points where pets can escape or intruders can enter.
Poor-quality fencing materials also tend to fade unevenly, develop gaps between panels, and sag noticeably – especially after exposure to harsh weather.
We’ve found that cheaper fasteners often fail, causing sections to separate or collapse. The repairs and replacements needed for these budget materials typically cost more over time than investing in quality materials from the start. Additionally, substandard fencing can reduce property value and create liability concerns. Inferior wood fencing is particularly susceptible to moisture damage and warping when not properly sealed or maintained.
Long-Term Maintenance Expenses for Cheap Fences
We’ve found that cheaper fencing options often require constant repairs, leading to maintenance costs that can exceed the initial savings within just a few years. What starts as minor fixes frequently evolves into major structural issues, forcing unexpected full replacements well before a quality fence would reach its end of life. Annual treatments for rust, rot, and degradation become increasingly necessary with budget materials, creating an ongoing expense that quality fences typically don’t demand until much later in their lifespan. Implementing proper regular maintenance routines with regular inspections and sealing can significantly extend even a budget fence’s useful life.
Regular Repairs Add Up
Although cheap fences may seem like a bargain initially, their ongoing repair costs can quickly surpass the price of a quality fence installation.
When we regularly need to address issues with lower-grade materials, we’re not just spending money – we’re investing time and effort into a continual cycle of repairs.
- Warped or split boards need replacement every 1-2 years, costing $15-30 per board
- Rusted fasteners require removal and replacement, often damaging surrounding materials
- Loose posts from inadequate concrete footings need re-setting at $100-200 per post
- Paint or stain touch-ups become necessary twice as often due to inferior wood quality
We’ll find ourselves making these repairs more frequently than with a premium fence, ultimately spending more money over the fence’s lifespan.
Hidden Replacement Costs Emerge
Beyond routine repairs, cheap fences harbor substantial hidden costs that surface over time. We’ll often discover that inferior materials require complete section replacements rather than simple fixes. When posts rot from subpar pressure treatment, we’re forced to replace not just the posts but also adjacent panels and hardware.
We’ve seen how cheap fencing’s structural issues can damage connected elements like gates and latches, creating a domino effect of replacements. Plus, when we need to match existing sections, discontinued or obsolete cheap fencing materials may force us to replace longer runs than necessary.
These unexpected costs compound when cheap fencing fails to meet local codes or HOA requirements, requiring wholesale upgrades. The true expense of bargain fencing reveals itself through these cascading replacement needs that weren’t apparent at installation.
Annual Treatment Requirements Increase
While quality fences require basic annual maintenance, cheap fencing demands increasingly frequent treatments to prevent rapid deterioration.
We’ve found that lower-quality materials need extensive care to combat accelerated wear, which drives up long-term ownership costs. As your trusted fencing professionals, we’ll help you understand the mounting maintenance requirements that cheap fences typically face.
- Water-seal treatments must be applied 2-3 times annually versus once for quality fences
- Anti-rust applications become necessary every 4-6 months as protective coatings fail
- Wood preservative treatments increase from annual to quarterly as materials degrade
- UV protective coatings need reapplication every 3-4 months to prevent warping and fading
Let’s work together to avoid these escalating maintenance demands by choosing materials that stand the test of time.
Why Professional Installation Matters for Fence Longevity
Despite their higher upfront cost, professionally installed fences deliver superior longevity compared to DIY installations. We’ve seen how proper installation techniques prevent common issues like post settling, gate sagging, and structural weakness that often plague amateur installations.
Professional fence contractors understand critical factors like proper post depth, concrete mixing ratios, and soil conditions that affect stability.
They’ll guarantee posts are set at the correct depth below the frost line, preventing frost heave damage in winter.
They also maintain precise spacing and alignment while accounting for ground slope variations.
Most importantly, pros have specialized tools and equipment to handle heavy materials safely and efficiently.
Their expertise with local building codes and utility line locations helps avoid costly mistakes that could compromise your fence’s integrity and safety over time.
With over two decades of experience, Texas Fence Company Katy has demonstrated how professional installation significantly extends fence lifespans through proper technique and premium materials.
Premium Fence Materials For Quality Fences That Stand the Test of Time
Professional installation must be paired with high-quality materials to achieve maximum fence durability.
We’ve learned that premium materials like vinyl, cedar, and wrought iron consistently outperform budget options in both aesthetics and longevity. When we invest in superior materials, we’re protecting our property value while reducing maintenance costs.
- Premium vinyl fencing features UV inhibitors and impact modifiers that prevent fading, cracking, and warping for 20+ years
- Western Red Cedar naturally resists rot, decay, and insect infestation due to its high content of protective compounds
- Hot-dip galvanized steel posts prevent underground corrosion and provide superior structural support
- Stainless steel fasteners and hardware eliminate rust streaking and maintain structural integrity in all weather conditions
The environmentally friendly vinyl offers exceptional sustainability by reducing deforestation while providing decades of maintenance-free performance.
Calculating Total Cost of Ownership for Your Fence
Although initial fence costs can be enticing, we’ve learned that the true expense goes far beyond the purchase price. When we calculate total ownership costs, we need to take into account maintenance requirements, repair frequency, and the fence’s expected lifespan.
Let’s factor in annual expenses like staining or painting, replacing damaged boards, and tightening loose hardware. For cheaper fences, we’ll typically spend more on repairs and face full replacement within 5-10 years. Quality fences, while costlier upfront, often last 20-30 years with minimal maintenance.
We must also account for labor costs, whether we’re handling maintenance ourselves or hiring professionals. By examining these long-term factors, we’ll make a more informed decision that saves money and frustration over our fence’s lifetime.
Vinyl fencing materials offer exceptional durability with minimal maintenance requirements, making them a cost-effective long-term investment despite higher upfront costs.
Signs Your Inexpensive Fence Is Failing Prematurely
When you’ve installed a low-cost fence, several telltale signs can indicate premature failure well before its expected lifespan.
Investing in budget fencing often means watching for early warning signs of failure, as problems frequently emerge sooner than expected.
We see these issues regularly in cheaper fencing materials and installations, which often lead to costly repairs or complete replacement.
- Posts begin to lean or shift position, especially after storms or soil saturation, indicating inadequate depth or poor foundation work
- Wood panels show splitting, warping, or extensive weather damage within the first year due to lower-grade materials
- Metal components develop rust spots or corrosion at connection points because of inferior protective coatings
- Gaps form between pickets or panels as fasteners loosen and materials shrink, compromising both security and appearance
Let’s examine these warning signs carefully – catching them early can help prevent more serious structural issues from developing.
Regular inspections throughout the year can identify these problems before they lead to costly structural damages that require complete replacement.
Smart Investment Strategies for Durable Fencing
Having seen the costly consequences of cutting corners with fencing, we can help you make smarter investment decisions that maximize long-term value.
We recommend focusing on high-grade materials like galvanized steel posts, pressure-treated lumber, and premium hardware that resist rust and decay.
It’s worth paying 20-30% more upfront for materials rated to last 20+ years. Build quality fences saves you in the long run.
Don’t overlook professional installation – proper post depth, concrete footings, and precise measurements are vital for structural integrity.
We suggest getting at least three detailed quotes from licensed contractors with proven track records.
To protect your investment, verify warranty coverage and maintenance requirements before purchasing.
Many manufacturers of quality fences offer 15-25 year warranties when installed by certified professionals.
Premium options like Western Red Cedar can last 15-20 years with minimal maintenance while naturally resisting decay and insects.
Frequently Asked Questions About Quality Fences
How Long Should I Wait Between Fence Staining or Painting Sessions?
We recommend staining or painting your fence every 2-3 years, but you’ll want to inspect it annually. Harsh weather conditions might require more frequent treatments to maintain ideal protection.
Can I Mix Different Fence Materials to Save Money?
We don’t recommend mixing fence materials, as it can create maintenance challenges, structural inconsistencies, and reduced property value. If you need to save money, we suggest phasing your fence installation instead.
What Are the Best Weather Conditions for Installing a Fence?
We’ll get the best fence installation results on dry days with temperatures between 50-80°F, minimal wind, and firm ground. Let’s avoid rainy conditions and frozen soil to guarantee proper post setting.
Do Certain Fence Styles Affect My Property’s Resale Value?
We’ve found that well-maintained wood, metal, or vinyl fencing can boost property value, while chain-link or basic panel fencing may decrease it. Privacy fences typically offer the highest return on investment.
Are There Specific Permits Required for Different Fence Heights?
We’ll need permits for quality fences over 6 feet tall in most jurisdictions, while lower fences typically don’t require them. Let’s check your local building codes for specific height regulations.
Takeaway
We’ve demonstrated that investing in quality fences and professional installation ultimately saves money over time. While budget options may seem attractive initially, they often lead to costly repairs, frequent maintenance, and premature replacement. By selecting premium materials and prioritizing proper installation, we’re ensuring our fences deliver lasting performance and value. Let’s make informed choices that protect our investment and reduce long-term ownership costs.