Pick the Right Fence for Your Home or Business
Picking the right fence for your project can be difficult. Property owners need to make numerous selections during the fence design process because each decision influences security measures and aesthetic appeal and property value. A strategic evaluation process which includes material selection and site-specific requirements and regulatory compliance determines the appropriate fence choice for commercial or residential areas. The process of choosing a suitable fence requires us to consider fundamental factors that will lead to an appropriate selection based on our needs and property improvements.
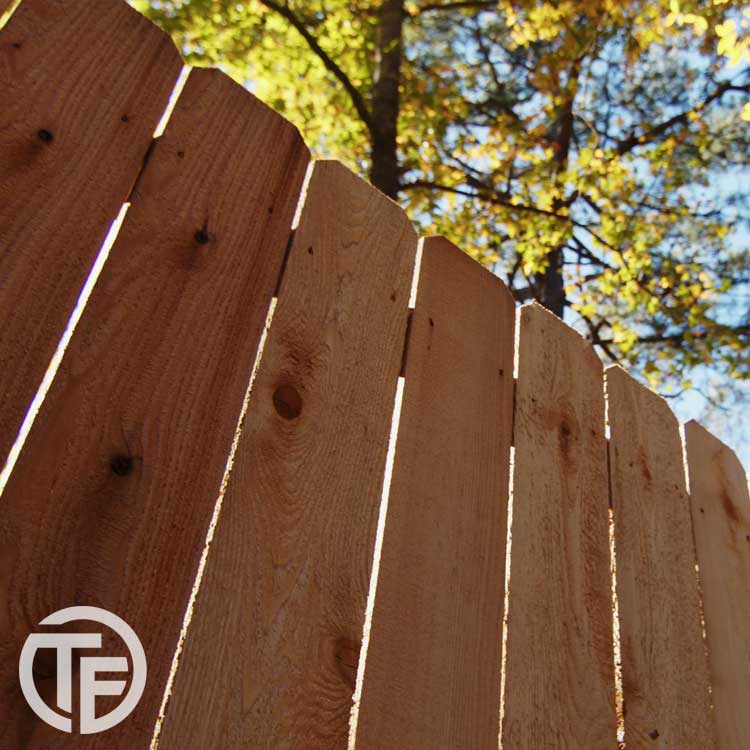
Key Points On Choosing the Right Fence
The best fence design emerges from an evaluation of your fundamental requirements between security needs and privacy needs and pet control and pool barrier requirements.
You must analyze local climate conditions together with terrain characteristics and soil type to pick fence materials which will provide optimal durability.
Before selecting your fence style and height you need to confirm compliance with local zoning laws and HOA restrictions and building codes.
The selection between wood vinyl metal and composite materials should be evaluated based on how much maintenance they need and their total cost-effectiveness throughout time.
To identify the best value for your budget you should evaluate both the expenses for initial installation and the costs of future maintenance.
Assessing Your Fencing Needs and Goals
Any successful fence installation requires first understanding the unique needs of a property.
Our evaluation process focuses on determining security requirements and privacy needs as well as local climate factors that will determine your fence design along with materials.
The first step involves determining your property’s main function since it determines the need for pet containment or pool safety or boundary establishment.
Our assessment will focus on your terrain’s features such as slopes together with soil types and present landscaping elements.
At this point in the process it becomes essential to understand all applicable zoning regulations and HOA restrictions.
The decision-making process involves identifying your ideal fence height and material strength requirements and maintenance needs within your budget limits.
The analysis will lead us to fence solutions that deliver sustained worth while addressing your specific property requirements.
HardiePlank and vinyl materials deliver outstanding durability for the challenging Houston weather.
Popular Fencing Materials and Their Benefits
We will analyze the four main fencing materials including wood metal vinyl and composite to assist you in selecting appropriate fencing for your property.
Homeowners who want classic fencing options can choose between wood types such as cedar, pine and redwood, while metal fencing includes durable aluminum along with traditional wrought iron and budget-friendly chain-link options.
The materials vinyl and composite provide weather-resistant options that do not need painting or staining for maintenance.
The cost-effectiveness of vinyl fencing stands out because it needs little maintenance while delivering years of durability.
Wood Fencing Options
Homeowners frequently choose wood fencing as their primary selection because it provides both natural aesthetic value and versatile design capabilities and numerous design choices. Our wood recommendations for building fences include cedar, redwood and pressure-treated pine. The natural decay and insect resistance of cedar and redwood wood types is matched by pressure-treated pine which provides durable performance at a lower price point.
The traditional look of picket fences suits traditional homes while board-on-board fences maximize privacy. The rustic appearance of split-rail fencing works best for big properties and shadowbox patterns create beautiful visual appeal from both sides of the fence.
Our selection of wood fencing materials needs to consider the regional climate because moisture conditions affect product longevity. Our investment needs protection from sealing and staining that requires maintenance every 2-3 years based on weather conditions.
Metal Fence Varieties
Metal fencing systems deliver high security along with durability while needing less upkeep than alternative building materials.
Our team will direct you to the best-selling metal fence types so you can select the right option for your property.
The lightweight strength and rust-resistant features of aluminum fencing make it suitable for both pool areas and decorative uses. The material exists in different forms and sizes and features powder-coated finishes which provide enduring protection.
The combination of steel fencing brings maximum security strength which suits commercial properties or high-security zones. You can select between wrought iron styles for traditional beauty and galvanized steel structures for industrial usage.
The low cost of chain link fencing allows customers to create their own customized designs. Vinyl-coated products have become available in various colors which both protect against corrosion and remain affordable.
Vinyl and Composite Materials
Modern vinyl and composite fencing materials combine durability features with low maintenance needs and various design possibilities to deliver exceptional value to customers. These materials achieve decades of protection against rot and rust and insect damage with minimal maintenance requirements.
We will analyze the benefits of choosing vinyl and composite materials. The variety of vinyl fences includes privacy panels as well as picket designs with multiple color options that stay vibrant without the need for painting. The combination of wood fibers with synthetic polymers in composite materials creates wooden appearances without exposing the wood to damage. The materials clean up with soap water and remain safe from splitting and extreme weather warping.
The environmentally friendly nature of these choices stems from their production methods that use recycled materials.
Understanding Local Regulations and Building Codes
The first step before starting any fence installation requires complete knowledge of the particular regulations and building codes which apply to your area.
It is crucial to contact your local building department prior to starting work to determine height limitations as well as setback standards and permit requirements.
The following regulations need your verification:
A professional survey must determine property lines and boundaries to prevent disputes about fence placement and ensure proper fence positioning.
HOA requirements along with neighborhood covenants specify rules for fence materials and styles as well as height limitations.
You should contact your local utility companies for their marking service to identify underground utility locations.
After confirming code compliance we can move on to material selection and installation planning.
The regulations between different jurisdictions differ significantly so what works in one area may be banned in another area.
Multiple fence companies should provide detailed written estimates to maintain project transparency and proper budgeting..
Cost Considerations and Budget Planning
A proper fence budgeting process demands thorough evaluation of various expenses which will significantly affect your final investment cost. Material expenses need to be accounted for because they differ significantly between wood, vinyl, aluminum and wrought iron choices.
Labor costs usually make up between 40-50% of the total bill yet surveys and permit fees will increase your budget by $200-500. Additional project costs should include post holes and concrete work together with hardware expenses and gate installation and finishing materials.
To prepare for potential issues we suggest adding a 10-15% contingency fund to handle unexpected problems like root removal and soil challenges. When measuring linear distance for your fence project remember to add extra materials because slopes and corners need additional materials. The supply industry provides financing options to customers while we can lower expenses through off-season installations and combining multiple property improvement services. The use of specialized tools for specific terrains in DIY projects will result in unexpected costs for your project.
Fence Styles and Design Options
The established budget parameters enable us to explore different fence styles that fulfill both financial needs and aesthetic preferences.
We will examine the most sought-after fence designs which unite durability with attractive design elements.
Traditional wooden fences provide enduring beauty through picket and split-rail and board-on-board construction methods which provide 25% to 100% privacy levels based on slat spacing and design choices.
Modern metal fencing includes wrought iron, aluminum, and steel varieties, featuring ornamental details, powder-coated finishes, and customizable heights from 3 to 8 feet.
The low-maintenance features of composite and vinyl solutions include rot resistance and rust resistance as well as paintless finishes which can be achieved in wood-grain appearances and various color schemes that match your property’s architectural style.
The distinct advantages of each style serve as decision-making tools to find the best solution for your particular requirements.
The durability and weather-resistance of vinyl fencing delivers superior long-term cost savings because it needs little maintenance to keep performing well.
Professional vs. DIY Installation
The selection between hiring contractors for professional fence installation and performing DIY installation depends on weighing initial contractor expenses against the time and equipment investment for self-installation.
The implementation of post hole diggers along with concrete mixers and power augers requires specialized tools that contractors already possess but DIY individuals must acquire or lease.
Professional installation expertise plays a crucial role because workers bring extensive knowledge of handling challenging terrain conditions together with utility line protocols and correct installation methods which guarantee enduring fence stability.
The selection of professional installation services provides quality materials and workmanship that ends up saving money on maintenance while extending the fence’s overall life expectancy.
Cost Vs Time Analysis
The choice between professional fence installation and DIY work needs thorough examination of both financial costs and time requirements.
DIY projects offer cost savings of 40-60% on labor expenses but homeowners must consider the costs of tool rentals along with material delivery charges and potential errors that need correction.
The price range for professional installation services runs from $15 to $50 per linear foot while delivering guaranteed work along with proper permits and utility marking services.
The total cost for DIY fence projects amounts to $10-30 per linear foot for materials and 20-40 hours of manual work depending on the fence style and ground elevation.
DIY installation expenses increase by $100 to $300 because of rental fees for post hole diggers and cement mixers.
The extra time spent on DIY work is typically worthwhile because it provides savings for basic fence designs that are installed on flat surfaces.
Professional services become the better long-term financial choice when dealing with intricate installation tasks or difficult terrain.
Tools and Expertise Required
The installation of fences by professionals demands specialized equipment together with specific expertise which typical homeowners lack but DIY fence projects need thorough evaluation of both necessary tools and individual skills.
We require post hole diggers, concrete mixers, levels, power tools along with precise measuring instruments to perform the installation correctly.
We need to determine our ability to operate heavy equipment as well as our knowledge of local building regulations when performing DIY installation tasks.
The process of self-installation requires either tool rental or purchase along with time dedicated to mastering correct installation methods.
Professional installers utilize their extensive experience along with their specialized equipment and efficient methods to achieve correct post depth measurements and proper spacing and alignment.
Before deciding between DIY installation and professional work we need to compare our technical skills with our tool access to the project’s complexity level.
Maintenance Requirements by Fence Type
Every fence type needs particular maintenance strategies to achieve both longevity and optimal performance.
An analysis of typical fence materials along with their upkeep requirements will assist you in developing a maintenance plan.
The regular maintenance of wood fences includes periodic sealing or staining every two to three years combined with inspections for rot or insect damage and quick replacement of broken boards.
We advise homeowners to check their nails annually and adjust the hardware if necessary.
The maintenance of metal fences including wrought iron and aluminum demands regular touch-up painting for scratch prevention as well as part lubrication and metal cleaner usage to stop oxidation.
The maintenance needs of vinyl fencing are minimal because regular soap and water cleaning prevents mildew formation.
We recommend checking for cracks or damage after severe weather events.
Proper drainage and waterproofing are essential for all fence types to prevent moisture-related deterioration and extend their lifespan.
Climate and Environmental Factors
The selection of fence material and design heavily depends on local environmental conditions and climate which affects both durability and required maintenance tasks.
We must analyze four essential environmental factors which include rainfall patterns together with humidity levels and UV exposure and soil composition and temperature changes.
We need to select materials that resist corrosion in coastal environments by using vinyl or aluminum to fight against salt spray. Regions that experience heavy snowfall require steel or pressure-treated wood as their materials for construction. We will include wind ports in our design or use open-design fencing when we encounter high wind conditions.
Let’s also consider your yard’s specific conditions.
The selection of rot-resistant materials is essential for properties that have poor drainage and the use of fencing that can resist damage from falling branches and extensive root systems in wooded areas.
Chain link fencing works effectively in different environments and weather conditions with low maintenance requirements.
Property Value Impact and Return on Investment
The selection of appropriate fencing materials leads to significant market value appreciation of your property.
The resale market recovery of quality fencing reaches 50-65% of initial investment costs which makes professional installation and material selection crucial decisions.
The combination of impact modifiers in High-quality PVC material makes vinyl fencing an excellent choice for lasting value.
Property value increases by 4-6% when installing privacy fences made from cedar or composite materials
Upscale neighborhoods prefer ornamental aluminum and wrought iron fences which enhance their appearance and fit with traditional architectural styles.
The combination of low maintenance expenses and young family attraction provides strong returns for well-maintained vinyl fencing in suburban areas.
We need to select a fence that fulfills present requirements while maximizing future market value in your particular location.
Frequently Asked Questions
How many days are required to complete an average fence installation from initial work until completion?
The duration of residential fence installation varies between one to three days based on property dimensions and site complexities and material selection and weather elements. Commercial projects require between 4 to 7 days for completion.
What is the correct procedure for installing a fence directly above existing concrete surfaces?
We do not support direct concrete installation since it creates instability problems. We need to core drill holes and set posts with concrete anchors or sleeves for proper fence support.
How close must fence posts be to each other to ensure maximum stability?
The best stability results from placing fence posts 6-8 feet apart although this may vary based on fence height and material selection. Our maximum post spacing for 6-foot privacy fences remains at 8 feet.
Will underground utility lines restrict the placement locations for my fence posts?
A call to 811 must be made before starting any fence post installation. They will identify underground utilities within 48-72 hours which provides us with safe areas to dig while protecting us from expensive and dangerous line damage.
Does the installation of your fence require prior notification to your neighbors?
It is essential to inform your neighbors before starting any fence installation work. It shows respect to neighbors and helps prevent conflicts and enables us to discuss boundary issues while building positive community ties.
Takeaway
We studied essential factors which will help you pick the right fence for your needs, including material selection and regulatory compliance. We can make better decisions by evaluating security needs together with climate conditions and maintenance requirements. The decision between professional installation and DIY work requires us to weigh initial expenses against lasting benefits. Our fence investment will support our property goals and follow local codes and HOA regulations.