Wood Fence Basics: Types, Maintenance, and Cost
When we’re planning to build a wood fence, we’re faced with numerous decisions that’ll shape both the functionality and aesthetics of our property for years to come. We’ll need to ponder various wood types, from budget-friendly pressure-treated pine to premium cedar and redwood options, along with multiple design styles that can complement our home’s architecture. While the initial investment might range from $15 to $50 per linear foot, making informed choices about materials, installation methods, and maintenance strategies will determine whether our fence lasts just a few years or stands strong for decades.
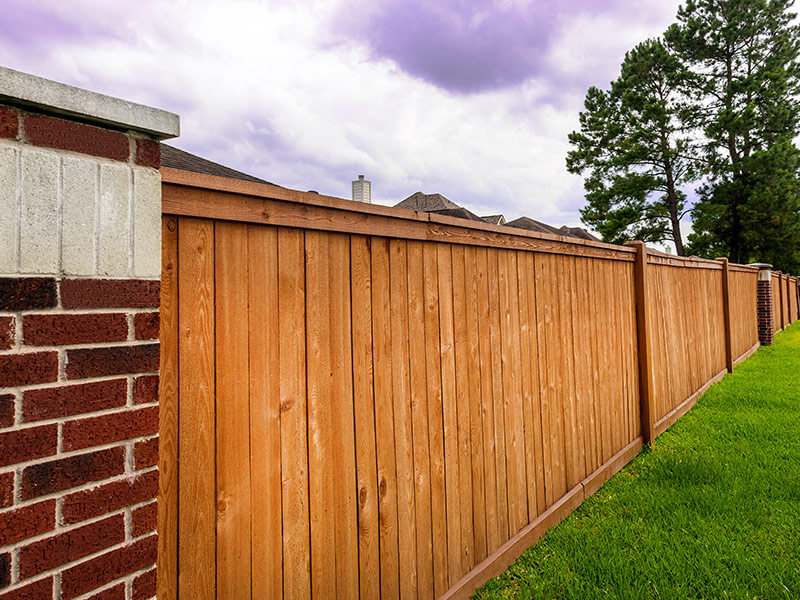
Key Points
- Common wood fence types include cedar, and redwood, each offering different benefits and appearances.
- Traditional privacy fencing, lattice-topped panels, and horizontal slat designs are popular styles that balance aesthetics with functionality.
- Installation requires proper planning, including property surveys, utility marking, and post holes dug at least 2 feet deep.
- Regular maintenance includes quarterly inspections, protective sealant applications every 2-3 years, and annual pressure washing to ensure 20+ years lifespan.
Types of Wood Fencing Materials
When it comes to wood fencing, not all materials are created equal—and at Texas Fence, we only use grade one materials to make sure your fence not only looks great but lasts for years.
There are several types of wood out there, and homeowners often hear names like pressure-treated pine, cedar, redwood, cypress, and Douglas fir. Each has its pros and cons, but we have a clear favorite.
Western Red Cedar is our #1 recommended choice for wood fences. It looks great, holds up well in our Texas weather, and naturally resists rot, moisture, and insects—thanks to the natural oils in the wood. It’s strong, beautiful, and built to last, which is why we stand behind it.
Other options include:
- Pressure-treated pine – This is the budget-friendly choice and holds up reasonably well, but it doesn’t offer the same appearance or long-term durability as Western Red Cedar.
- Redwood – It looks sharp and holds up great, but it tends to be on the pricey side.
- Cypress – Known for repelling insects, it’s solid but not as commonly used in our area.
- Douglas fir – A strong pick often used for posts and rails, but it doesn’t offer the same weather resistance.
No matter which wood you choose, we make sure it’s top-grade material. But if you want a wood fence that’s built to stand out and stand strong, you really can’t beat Western Red Cedar.
Popular Wood Fence Styles
When it comes to wood fence styles, we’ll explore both classic privacy designs and modern decorative variations that fit different budgets.
Traditional privacy fencing often features 6-foot stockade or board-on-board configurations that maximize security and screening.
Contemporary options include lattice-topped panels, horizontal slat designs, and shadowbox patterns that combine aesthetics with varying levels of privacy.
These enclosures can create serene outdoor havens perfect for undisturbed relaxation and retreat spaces.
Traditional Privacy Designs
Traditional wood privacy fences offer several time-tested designs that combine aesthetics with function. We commonly see the board-on-board style, where fence boards overlap slightly to eliminate gaps and guarantee complete privacy.
The classic stockade design features boards placed tightly together, while the shadow box pattern creates visual interest from both sides using alternating boards.
For maximum durability, we recommend 6×6 posts set in concrete at 6-8 feet intervals, with horizontal rails connecting them. Cedar and pressure-treated pine remain popular choices, balancing cost with longevity. Most privacy fences range from 6 to 8 feet tall, meeting standard residential codes while providing ideal screening.
Adding a lattice top or decorative post caps can enhance curb appeal without compromising the fence’s primary security function.
Contemporary Decorative Options
Modern wood fence designs embrace sleek horizontal layouts and mixed material combinations that can transform an ordinary boundary into an architectural focal point. We’re seeing trends toward board-on-board horizontal installations, often paired with powder-coated metal posts or decorative concrete elements. These contemporary styles typically cost 15-25% more than traditional vertical designs.
Popular options include shadowbox patterns with alternating depths, floating slat designs with calculated gaps, and geometric panel inserts that create stunning light and shadow effects. We can achieve sophisticated looks by incorporating cedar or other woods with black aluminum frames. For budget-conscious homeowners, pressure-treated pine arranged in modern patterns offers a similar aesthetic at half the cost. LED lighting integration and living wall elements are gaining traction, allowing us to customize these contemporary installations for both privacy and style.
Planning Your Wood Fence Project
Before starting your fence installation, proper planning will save significant time and money while ensuring compliance with local regulations. We’ll need to survey property lines, mark utility locations, and determine post spacing based on local soil conditions. Let’s calculate materials needed, including posts, rails, pickets, concrete, and hardware, adding 10% for waste.
- Nothing’s more frustrating than hitting a utility line because we skipped the call to 811
- We’ve all seen that neighbor’s fence that violates setback rules and had to be torn down
- You’ll feel confident knowing every post hole meets frost line requirements
- There’s pride in showing friends a perfectly straight fence line that’s built to code
Consider wind loads, drainage patterns, and grade changes when positioning your fence. We’ll need to secure permits and verify HOA guidelines before breaking ground. For optimal stability, ensure post hole depth equals at least one-third of the total post length.
Installation Best Practices
Installing a wood fence correctly requires attention to core fundamentals that guarantee structural integrity and longevity. We’ll guide you through essential best practices that safeguard your investment stands the test of time.
Task | Critical Points | Common Pitfalls |
---|---|---|
Post Holes | 2ft depth minimum | Shallow placement |
Concrete Mix | 4:1 ratio mix | Incorrect mixing |
Post Spacing | 6-8ft intervals | Uneven spans |
Gate Support | Double reinforcement | Insufficient bracing |
Let’s start with proper post installation – the foundation of every successful fence project. We’ll want to dig holes one-third the height of our posts, use crushed gravel for drainage, and secure posts are perfectly plumb. Quality hardware and pressure-treated lumber are non-negotiable elements that prevent premature rot and structural failure. Using galvanized hardware helps ensure maximum durability against rust and weather exposure.
Maintaining Your Wood Fence
While initial installation sets the foundation, proper maintenance determines your wood fence’s ultimate lifespan and aesthetic appeal. We recommend conducting quarterly inspections and addressing issues promptly to prevent costly repairs. Apply a protective sealant every 2-3 years, using high-grade water repellent products specifically formulated for exterior wood. Replace damaged boards and rusted hardware immediately to maintain structural integrity. Regular UV-resistant stain applications will help protect your fence from sun damage and fading.
- Feel confident knowing you’re protecting your property investment with each maintenance task
- Join other homeowners who take pride in their well-maintained fencing
- Rest assured that your family’s privacy and security remain intact
- Experience satisfaction as your fence continues to enhance your home’s curb appeal
Remember to pressure wash annually, maintain proper drainage along the fence line, and trim vegetation that could trap moisture against the wood.
Cost and Budget Considerations
While initial fence installation costs can range from $25-55 per linear foot depending on material grade and labor rates, we’ll need to factor in permits, hardware, gates, and site preparation into our total project budget.
We’re seeing pressure-treated pine emerge as the most cost-effective wood option, offering 15-20 years of service life with proper maintenance. When we analyze long-term value, it’s vital to ponder annual maintenance costs of $2-4 per linear foot against the durability and aesthetic benefits that wood fencing delivers.
The rot-resistant properties of pressure-treated pine make it a superior investment compared to untreated wood options, particularly in regions with high moisture levels.
Initial Installation Costs
Building a wood fence requires careful budgeting, as initial installation costs can range from $30 to $70 per linear foot, depending on material quality and local labor rates. We’ll need to factor in several cost components, including materials, labor, permits, and equipment rentals. Professional installation typically accounts for 50% of the total project cost, while materials make up the remaining portion.
Imagine the pride of investing in premium cedar that’ll last decades longer than basic pine. Feel confident knowing you’ve protected your property with proper post-setting depths. Experience peace of mind with professional-grade hardware and concrete footings. Join countless homeowners who’ve enhanced their property values through quality fencing.
When calculating installation costs, we must consider site preparation, post hole digging, concrete work, and the complexity of your yard’s terrain.
Long-Term Value Analysis
To accurately assess a wood fence’s value proposition, we’ll need to examine costs beyond the initial installation. Let’s analyze the long-term investment factors that impact our total ownership costs over a typical 20-year lifecycle.
Cost Factor | Average Impact |
---|---|
Annual Maintenance | $100-300 |
Repairs (per incident) | $200-500 |
Staining/Sealing | $700-1,200 |
Replacement Parts | $150-400 |
When we factor in regular upkeep, a quality wood fence typically delivers strong ROI through enhanced property value and extended service life. While cedar and pressure-treated pine require different maintenance schedules, both offer excellent durability when properly maintained. By budgeting $300-500 annually for preservation, we’re protecting our investment and maximizing the fence’s longevity.
Frequently Asked Questions
Can My Existing Fence Posts Be Reused When Installing a New Fence?
We’ll need to inspect your existing posts for rot, cracks, and proper anchoring. If they’re structurally sound and correctly positioned, reusing them can save significant costs on your installation project.
How Long Should I Wait Before Staining or Painting a New Fence?
We recommend waiting 2-4 weeks for pressure-treated lumber to dry completely before applying stain or paint. Moisture content should test below 15% using a wood meter for ideal results.
What’s the Ideal Distance Between My Fence and Nearby Trees’ Trunks?
We recommend placing fences at least 3-5 feet from mature tree trunks, allowing for root growth and preventing structural damage. For saplings, we’ll want 8-10 feet to accommodate future expansion.
Do I Need to Notify My Utility Company Before Digging Fence Posts?
We must call 811 or our local utilities at least 48-72 hours before digging. They’ll mark underground lines free of charge, protecting us from costly repairs and dangerous accidents.
How Much Gap Should I Leave Between Fence Boards for Expansion?
We recommend leaving a 1/8 to 1/4 inch gap between fence boards to accommodate seasonal wood expansion and contraction. This spacing also helps prevent warping and promotes proper airflow through your fence.
Takeaway
We’ve explored essential aspects of wood fence installation, from material selection to maintenance protocols. By factoring in the cost-benefit analysis of premium woods like cedar versus pressure-treated options, and understanding ROI implications, we can make informed decisions for our fencing projects. Through proper planning, professional installation, and preventive maintenance scheduling, we’ll optimize our fence’s longevity and protect our investment over its service life.