Fence Installation: Texas Fence
Just as Rome wasn’t built in a day, we can’t expect to throw up a fence without proper planning and know-how. We’ve seen countless DIY fence projects go sideways because homeowners rush into installation without considering pivotal factors like permits, property lines, and proper post-setting techniques. Whether you’re looking to create privacy, enhance security, or boost curb appeal, we’ll guide you through the essential steps that separate successful fence installations from expensive mistakes. Let’s explore what it takes to build a fence that’ll stand the test of time and serve its intended purpose.
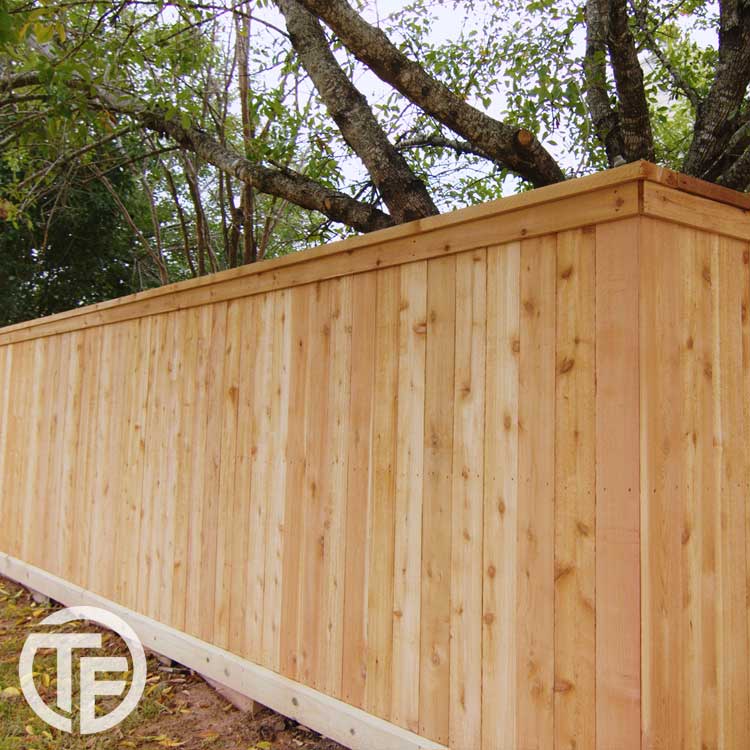
Key Points
- Begin by checking local regulations, obtaining necessary permits, and conducting a property survey to confirm boundary lines.
- Choose appropriate fencing material based on purpose, budget, and maintenance requirements among wood, vinyl, aluminum, or chain link options.
- Dig post holes 6 inches below frost line, use concrete for stability, and ensure posts are level and properly spaced.
- Install horizontal rails securely between posts, maintaining proper alignment before attaching fence panels with appropriate fasteners.
- Complete fence installation by adding gates with proper hardware, ensuring smooth operation and secure latching mechanisms.
Planning Your Fence Project
Successfully planning a fence installation requires careful consideration of several key factors before breaking ground. We’ll need to start by checking local zoning laws, HOA regulations, and obtaining necessary permits to guarantee our project meets all requirements. It’s also essential that we locate property lines and underground utilities through proper surveys and marking services. Next, we’ll determine the fence’s purpose – whether it’s for privacy, security, pool safety, or property definition – as this influences material selection and design specifications.
We must consider factors like height restrictions, post spacing, and gate locations while accounting for terrain challenges and drainage patterns. HOA guidelines often include specific regulations regarding size, style, and construction materials for fences. Let’s evaluate material options based on our climate, maintenance preferences, and budget constraints. Wood offers traditional appeal but requires upkeep, while vinyl provides durability with minimal maintenance. Aluminum and wrought iron deliver security with elegance, and chain-link remains cost-effective for basic boundary needs. We’ll create a detailed materials list, including posts, panels, concrete, hardware, and tools. By measuring accurately and adding 10% for waste, we’ll prevent costly mid-project supply runs. Finally, we’ll establish a realistic timeline that accounts for weather conditions and inspection schedules.
Types of Fencing Materials
Each fencing material brings distinct advantages and specific applications to your fence project. Let’s explore the most common options we’ve found successful for residential and commercial installations, helping you make an informed decision that aligns with your needs.
Material | Key Benefits |
---|---|
Wood | Natural appearance, cost-effective, easily customizable |
Vinyl | Low maintenance, weather-resistant, long lifespan |
Aluminum | Lightweight, rust-resistant, ideal for slopes |
Chain Link | Economical, durable, perfect for security |
We’ve noticed that wood remains popular for its traditional appeal and affordability, though it requires regular maintenance to prevent rot and insect damage. Vinyl’s gaining traction because it’s virtually maintenance-free and won’t splinter or fade. When we’re working with challenging terrain, aluminum’s our go-to choice since it’s adaptable and won’t corrode. Chain link’s still the most practical option for large areas where security’s the primary concern.
Vinyl fencing provides excellent privacy with tightly spaced panels and no visible gaps, enhancing property value by ensuring security and seclusion.
Before making your selection, we’ll need to study your climate, budget, maintenance preferences, and intended use. Each material requires different installation techniques, and we’ll guarantee you understand the long-term implications of your choice.
Local Regulations and Permits
Before breaking ground on any fence installation, you’ll need to navigate your local municipality’s regulations and secure the necessary permits. Let’s walk through the essential steps to guarantee we’re in full compliance with local laws and avoid costly penalties or mandatory fence removal.
First, we’ll need to contact our local building department or planning office to understand specific requirements. Most municipalities regulate fence height, setback distances from property lines, and material restrictions. We’ll also need to verify whether we’re subject to any homeowners’ association (HOA) guidelines that might impose additional limitations.
Next, we’ll want to schedule a property survey to confirm exact boundary lines and mark underground utilities. Many jurisdictions require this documentation with the permit application. We’ll submit detailed plans showing fence location, height, materials, and post-hole specifications. Typical permit fees range from $50 to $300, depending on location and project scope.
Once approved, we’ll display our permit prominently during construction. Remember to schedule required inspections throughout the installation process, particularly for post-hole depth and final completion verification. These inspections protect us and validate our compliance with local codes. It’s also essential to consider aesthetic consistency in neighborhoods where uniform fence appearance is enforced by HOA guidelines.
Property Line Considerations
Property lines serve as the foundation for any fence installation project, and proper boundary determination can prevent future disputes with neighbors. When we’re planning a fence installation, we’ll need to be absolutely certain about property boundaries through official documentation and professional surveys. Let’s work together to guarantee we’re building on the correct side of the line and maintaining positive relationships with adjacent property owners.
Before breaking ground, we need to complete these essential steps:
- Obtain a current property survey from a licensed surveyor, or locate your existing survey documentation from when you purchased your property
- Mark your property corners with stakes and run Mason’s line to visualize the exact boundary path
- Consult with neighbors about your fencing plans and get written agreement on shared boundary lines
- Offset the fence installation slightly inside your property line (typically 2-4 inches) to ascertain no encroachment
Remember that we’re legally responsible for accurate placement, and moving a fence after installation is extremely costly. If there’s any uncertainty about boundary locations, we should always invest in professional surveying services before proceeding with installation. Understanding shared responsibility for fence maintenance can also help in maintaining amicable relationships with neighbors.
Tools and Equipment Needed
To pull off a professional fence installation, we’ll need a thorough set of tools and equipment that balance precision with efficiency. Let’s break down our essential gear into categories that will guarantee we’re well-prepared for every phase of the project.
Tool Category | Essential Items |
---|---|
Digging & Post Setting | Post hole digger, shovel, manual/power auger, level |
Measuring & Layout | Tape measure, string line, marking paint, stakes |
Cutting & Assembly | Circular saw, drill/driver, hammer, post level |
We’ll want to gather these tools before starting to avoid delays mid-project. For power tools, it’s critical to have backup batteries or extension cords ready. Don’t forget personal protective equipment (PPE) including work gloves, safety glasses, and steel-toed boots. If we’re working with concrete for post setting, we’ll also need a wheelbarrow, mixing tub, and concrete tools. For specialized fencing materials like vinyl or metal, we might require additional tools specific to those materials, such as tin snips or specialized brackets. Remember, investing in quality tools now will save us time and frustration throughout the installation process. Professional companies use high-grade materials to ensure the longevity and quality of the fence.
Setting Fence Posts
Let’s install fence posts properly by following standard depth requirements – typically one-third of the post’s height plus an extra 6 inches below the frost line.
We’ll start by mixing concrete to the right consistency, combining one part cement, two parts sand, and three parts gravel with water until it reaches a thick, workable texture.
Once we’ve got our mixture ready, we’ll pour it into each post hole, ensuring the posts remain perfectly plumb while the concrete sets.
For fence stability(Plan Before You Put Up Those Pickets), it’s crucial to consider soil conditions and ensure proper anchoring to prevent shifting over time.
Post Depth Requirements
Setting fence posts at the correct depth is vital for long-term stability and structural integrity. We’ll help you determine the proper depth requirements to safeguard your fence stands strong for years to come. The general rule is that one-third of the total post length should be underground, but several factors influence the exact depth needed.
Local building codes, soil conditions, and fence height all play pivotal roles in determining post depth. In areas with loose or sandy soil, we’ll need to dig deeper
Concrete Mixing Steps
With the post holes properly dug to specifications, we’ll focus on mixing the concrete that will permanently secure your fence posts. Let’s start by gathering our materials: fast-setting concrete mix, clean water, a wheelbarrow, and a mixing hoe. We’ll need roughly two 50-pound bags of concrete per post hole for standard residential fencing.
Pour one bag of concrete mix into the wheelbarrow, then create a small depression in the center. We’ll add water gradually, using approximately 1 gallon per 50-pound bag. Mix thoroughly with the hoe, working from the outside edges toward the center. The consistency should resemble thick oatmeal – not too wet or too dry. When you can form a ball that holds its shape without crumbling or being soupy, you’ve achieved the right mix.
Don’t mix more concrete than you can use in about 20 minutes, as it begins setting quickly. Once we’ve achieved the proper consistency, we’ll immediately pour the mixture into the post hole, filling it to about 2-3 inches below ground level. This allows for soil coverage while providing maximum stability for your fence posts.
Installing Rails and Panels
Let’s address the key aspects of installing rails and panels to build a strong, lasting fence. We’ll first attach horizontal rails securely to our posts using appropriate fasteners and spacing to create the framework, ensuring proper leveling and alignment throughout.
We’ll then mount the fence panels, maintaining consistent spacing between components while checking for proper vertical alignment and structural integrity.
Attaching Rails to Posts
The installation of rails and panels represents the most complex phase of fence construction, requiring precise measurements and proper attachment techniques. We’ll secure the rails to our posts using galvanized brackets and screws, verifying a sturdy connection that withstands weather and time.
When attaching rails, we’ll follow these critical steps to maintain structural integrity:
- Position the bottom rail first, securing it 6 inches above ground level using temporary supports and a level to validate perfect alignment before final attachment
- Install brackets at marked heights on the posts, pre-drilling holes to prevent wood splitting and using manufacturer-specified fasteners for ideal strength
- Set the top rail in place, checking for level across multiple posts while maintaining consistent spacing from the bottom rail
- Secure middle rails (if required) at equal intervals between top and bottom rails, using a measuring tape to confirm uniform spacing
Let’s double-check all connections, confirming screws are flush and brackets are firmly attached. A properly secured rail system provides the foundation for panel installation and guarantees our fence’s long-term stability.
Securing Panel Components
Now that our rails are firmly attached, installing the fence panels requires careful attention to proper securing techniques and spacing. Let’s start by measuring and marking equal spacing between panels, leaving a 1/8-inch gap for expansion. We’ll use a level and spacer blocks to maintain consistent positioning as we work.
For wooden panels, we’ll secure them using 2½-inch deck screws, placing two screws at each rail intersection. When working with vinyl or composite panels, we’ll need to use manufacturer-recommended fasteners and follow their specific spacing requirements. It’s imperative that we pre-drill holes to prevent splitting and guarantee proper alignment.
As we install each panel, we’ll check for plumb using our level and adjust as needed before final securing. We’ll work systematically from one end to the other, continually verifying our measurements and spacing.
For areas where we need to cut panels, we’ll use a circular saw with the appropriate blade, making sure to seal any exposed edges with a protective coating. Remember to periodically step back and verify that our sight line remains straight and our panels are uniformly secured.
Panel Spacing and Alignment
Proper panel spacing and alignment serve as critical foundations for a professional fence installation. We’ll guarantee each panel maintains uniform spacing and precise vertical alignment to create a cohesive, stable structure. Let’s focus on achieving consistent gaps between panels that accommodate natural material expansion while maintaining security and aesthetics.
Apply our 3-4-5 triangle method to establish perfect right angles at corners, measuring carefully from your base points to ascertain panels remain square with property lines. Position each panel using temporary braces and a level, maintaining a consistent 1/8″ to 1/4″ gap between panels to allow for seasonal movement. Verify plumb on both sides of each panel using a 4-foot level, adjusting the braces as needed before final attachment. Work systematically down the fence line, checking measurements every 8-10 feet to prevent cumulative spacing errors.
After securing each panel, we’ll double-check our spacing measurements and make micro-adjustments as needed. Remember to account for grade changes by stepping or sloping panels appropriately, maintaining level tops unless the design specifies otherwise. This attention to spacing and alignment will guarantee your fence stands straight and true for years to come.
Gate Installation and Hardware
Installing a gate requires careful planning and precise measurements to guarantee smooth operation and longevity. We’ll need to ascertain our posts are set extra deep and reinforced with concrete to handle the added weight and movement.
Let’s position the hinges at least 6 inches from the top and bottom of the gate post, using heavy-duty hardware rated for the gate’s weight.
For a standard walk-through gate, we’ll maintain a 1/2-inch gap between the gate and posts, and 2 inches of ground clearance to prevent dragging. We’ll install the latch mechanism at a comfortable height of 36-48 inches, making sure it aligns perfectly with the catch.
If we’re working with a double gate, we’ll add a drop rod or cane bolt for additional stability when closed.
To prevent sagging, we’ll install a diagonal brace running from the top hinge corner to the bottom latch corner. We’ll also add gate stops to limit the swing range and protect our hinges. Automatic gates ensure secure closure after each use, providing enhanced safety and reducing the risk of unwanted access. Finally, we’ll adjust the hinges to achieve proper alignment and test the gate’s operation multiple times before considering the job complete.
Maintenance and Care Tips
Regular maintenance guarantees your fence’s longevity and structural integrity for years to come. We recommend establishing a routine inspection schedule to identify and address potential issues before they become serious problems.
Let’s walk through essential maintenance practices that’ll keep your fence in top condition.
- Clean your fence annually using appropriate cleaning solutions – pressure washing for vinyl and metal fences, wood cleaner for wooden fences, and mild soap solutions for wrought iron. Remove dirt, moss, and debris that can trap moisture and cause deterioration.
- Inspect for loose posts, hardware, and damaged sections every six months. We’ll want to tighten any loose screws, replace rusted hardware, and repair damaged boards promptly to prevent further structural issues.
- Apply protective coatings as needed – wood fences require sealing or staining every 2-3 years, while metal fences benefit from rust-resistant paint touch-ups when scratches appear.
- Maintain proper drainage around fence posts by ensuring soil grade slopes away from the fence. Clear vegetation growth and trim branches that could damage your fence during storms.
- For metal fences, rust prevention is essential to maintain fence integrity and longevity. Regularly inspect for rust spots and treat them with a corrosion-resistant coating to prevent further damage.
Frequently Asked Questions
Can I Install a Fence on Uneven or Sloped Terrain?
Yes, we can install fences on sloped terrain by stepping or racking the panels to follow the grade, ensuring each section remains level while adapting to the changing elevation of your land.
Will My Homeowner’s Insurance Rates Change After Installing a Fence?
You’ll be thrilled to hear that we typically see minimal impact on insurance rates. We recommend checking with your provider, as fences can actually lower premiums by improving security and safety.
How Do Underground Utilities Affect the Depth of Fence Post Holes?
We’ll need to adjust post hole depths around utilities, typically keeping holes at least 12 inches away and sometimes shallower. Let’s always call 811 before digging to locate underground lines.
What’s the Best Time of Year to Install a New Fence?
Like planting a garden, we’ll get the best results in spring or fall when soil’s workable and weather’s mild. Let’s avoid frozen ground or summer’s intense heat for easier digging.
How Long Should I Wait Before Painting or Staining a New Fence?
We recommend waiting 30-60 days before painting or staining a new wooden fence. This allows the wood to properly dry and accept finishes, ensuring better protection and longevity.
Takeaway
We’ve walked through the essentials of fence installation like seasoned pros, covering everything from initial planning to final maintenance. Like building a house of cards, each step must be precise and purposeful. By following proper techniques for post-setting, material selection, and assembly, while adhering to local regulations, we’ll guarantee a fence that stands strong for years. Regular maintenance keeps our investment secure and visually appealing.